In the realm of industrial processes, welding stands as an indispensable technique, melding metals together with precision and strength. Yet, amidst the sparks and heat, lurks an often-overlooked danger: welding hazards fumes and gases. These seemingly innocuous byproducts pose significant threats to both machinery and human health, warranting our attention and action.
Impacts on Machinery and Equipment:
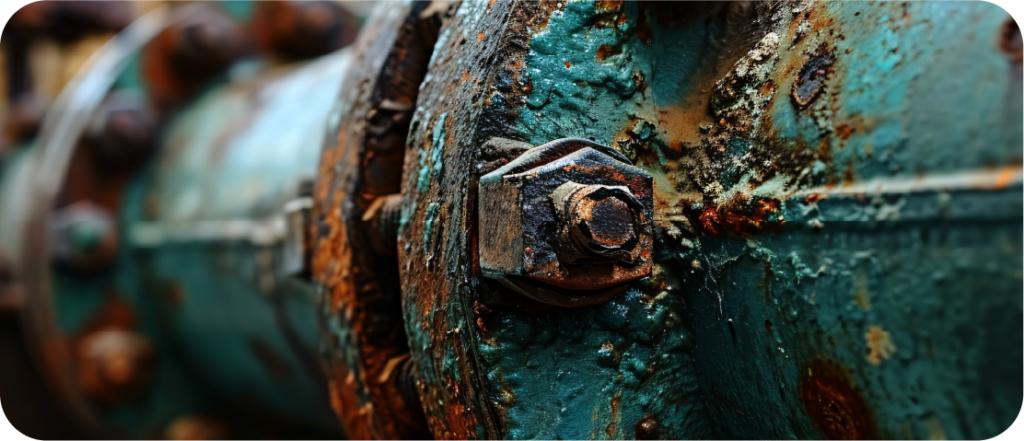
Welding fumes and gases can corrode and deteriorate machinery and equipment over time. The acidic nature of certain contaminants accelerates the degradation of metal surfaces, leading to premature wear and tear, compromised structural integrity, and ultimately, equipment failure. From industrial robots to welding torches, no component is immune to the corrosive effects of welding emissions.
Moreover, the presence of welding hazards like fumes and gases in the ambient environment poses risks to sensitive electronic equipment and machinery. Particulate matter can infiltrate intricate circuits and mechanisms, disrupting operations and diminishing performance. The accumulation of contaminants on surfaces further exacerbates maintenance challenges, necessitating costly repairs and replacements.
Here are some complications or physical issues that machinery and equipment can experience due to exposure to welding fumes and gases:
- Corrosion of metal surfaces: Welding fumes and gases, particularly those containing acidic compounds, can accelerate the corrosion of metal surfaces, leading to premature deterioration and structural weakness.
- Increased wear and tear: The presence of contaminants in the air can contribute to increased friction and abrasion within machinery components, resulting in accelerated wear and tear over time.
- Degradation of electrical systems: Particulate matter from welding fumes can infiltrate electrical systems and components, causing insulation breakdown, short circuits, and other electrical failures.
- Fouling of cooling systems: Welding fumes and gases can accumulate in cooling systems, obstructing heat transfer and reducing the efficiency of cooling mechanisms, leading to overheating and potential damage.
- Contamination of lubricants: Contaminants from welding emissions can infiltrate lubrication systems, compromising the effectiveness of lubricants and resulting in increased friction and component failure.
- Impairment of sensitive equipment: Sensitive electronic equipment and instrumentation may be adversely affected by exposure to welding fumes and gases, leading to malfunctions, calibration errors, and data inaccuracies.
- Erosion of surface finishes: Welding contaminants can erode surface finishes and coatings, diminishing aesthetic appeal and exposing underlying materials to further degradation.
These complications highlight the importance of implementing effective measures to control welding emissions and protect machinery and equipment from the adverse effects of exposure. By investing in proper ventilation, filtration, and maintenance strategies, businesses can minimize the risks associated with welding operations and prolong the lifespan of their assets.
Impacts on Human Health:
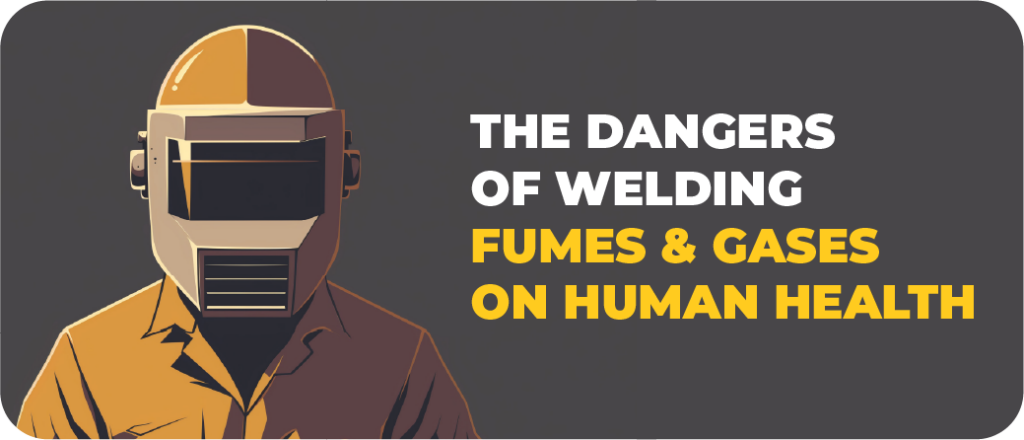
Welding generates a plethora of airborne contaminants, including particulate matter and toxic gases such as ozone, nitrogen oxides, and carbon monoxide. Prolonged exposure to these substances can lead to various complications and physical issues among welders, including:
- Respiratory Ailments: Welders frequently suffer from respiratory issues such as coughing, wheezing, and shortness of breath due to the inhalation of welding fumes. These pollutants can irritate the airways, leading to conditions like bronchitis and pneumonitis, and exacerbating pre-existing respiratory conditions such as asthma and chronic obstructive pulmonary disease (COPD).
- Lung Irritation: The inhalation of welding fumes can cause acute irritation to the lungs, leading to symptoms such as chest tightness, coughing up phlegm, and difficulty breathing. Prolonged exposure may result in chronic lung irritation, increasing the risk of respiratory infections and long-term lung damage.
- Metal Fume Fever: Welders exposed to certain metal fumes, such as zinc, aluminum, and magnesium, may experience symptoms of metal fume fever. This condition typically presents with flu-like symptoms, including fever, chills, headache, fatigue, and muscle aches, and usually resolves within 24 to 48 hours.
- Neurological Disorders: Some welding fumes contain neurotoxic substances, such as manganese and lead, which can adversely affect the nervous system. Chronic exposure to these toxins may lead to neurological disorders, including tremors, cognitive impairment, and Parkinson’s disease-like symptoms.
- Reproductive Complications: Female welders exposed to welding fumes and gases may face reproductive health risks, including miscarriage, preterm birth, and birth defects. Male welders may experience reduced fertility and an increased risk of reproductive abnormalities in offspring due to exposure to certain metals and chemicals.
These complications underscore the importance of implementing effective measures to control exposure to welding hazards like fumes and gases, including proper ventilation, use of personal protective equipment (PPE), and regular health monitoring for welders. By prioritizing worker safety and health, businesses can mitigate the risks associated with welding operations and promote a healthier work environment.
Protecting Against Welding Hazards: Plymovent Solutions:
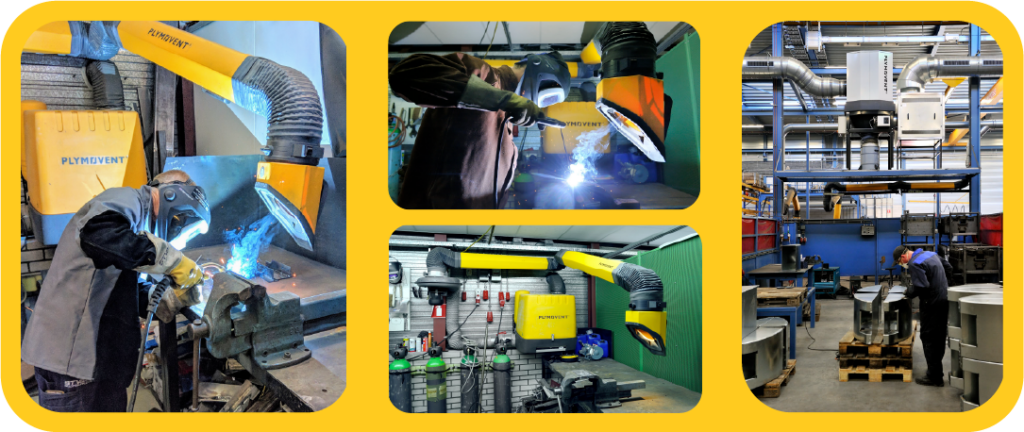
At Plymovent, we have been at the forefront of the ventilation business since 1975, serving both industrial giants and individual users alike. With a rich history of innovation and excellence, we have established ourselves as the premier solution provider for all ventilation needs.
By addressing the dual challenges of human health risks and machinery degradation, Plymovent Solutions offers comprehensive protection for industries and their workforce. From advanced fume extraction systems to state-of-the-art filtration technology, Plymovent equips businesses with the tools they need to navigate welding hazards with confidence and peace of mind.
Our extensive range of products caters to diverse requirements, offering a plethora of options whether you seek mobile solutions or wall-mounted units. From compact designs to robust industrial-grade systems, Plymovent delivers tailor-made solutions to suit every environment.
We take pride in our ability to provide custom solutions, crafted precisely to meet your unique needs and specifications. With a track record of assisting over 50,000 industries and countless individual customers, Plymovent is synonymous with reliability, quality, and top-notch service.
When you choose Plymovent, you’re not just investing in a product – you’re investing in peace of mind. Experience the difference with Plymovent, where excellence meets innovation, and customer satisfaction is our top priority.
Discover our range of portable extractors: https://bit.ly/43gDTKZ and https://bit.ly/49Vf49Q
Comments are closed.