In recent years, robotic arms have revolutionized welding in manufacturing industries, offering efficiency, precision, and consistency. However, despite their technological advancements, these machines are not immune to the detrimental effects of welding fumes. Here, we explore the challenges posed by welding fumes to robotic arms and the broader implications for industrial operations.
Understanding the Hazard: Welding Fumes
Welding fumes are a complex mixture of airborne particles and gases generated during welding processes. These fumes can contain hazardous substances such as metals (e.g., chromium, manganese), gases (e.g., carbon monoxide), and particulates, posing health risks to human welders. Similarly, these fumes can adversely affect robotic arms, albeit in different ways.
Rust and Corrosion
Robotic arms used in welding applications are often exposed to heat, sparks, and metal particulates released during the welding process. Over time, these particles settle on the arm’s surfaces, potentially leading to rust and corrosion. Rust can degrade the structural integrity of the robotic arm, affecting its movement and performance. Moreover, corrosion can compromise sensitive electronic components, leading to malfunction or failure.
Accumulation in Joints and Mechanisms
Welding fumes can accumulate in the joints, gears, and other mechanical components of robotic arms. This accumulation may impede smooth movement and operation, causing stiffness or reduced range of motion. Over time, buildup can lead to increased friction, accelerated wear, and ultimately, mechanical failure if not adequately maintained and cleaned.
Electronic and Sensor Interference
Modern robotic arms rely heavily on advanced electronic sensors and controllers for precise welding operations. However, welding fumes can infiltrate these sensitive components, causing electrical interference or short-circuiting. Contaminants from welding fumes may also compromise optical sensors and vision systems used for guidance and positioning, affecting the arm’s accuracy and reliability.
Maintenance Challenges
Maintaining robotic arms in welding environments becomes challenging due to the constant exposure to welding fumes. Regular cleaning and maintenance are crucial to prevent rust, corrosion, and buildup in mechanical and electronic components. However, these tasks require specialized knowledge and resources, adding to operational costs and downtime.
Mitigating the Risks: Cost Savings and Operational Improvements
To mitigate the adverse effects of welding fumes on robotic arms, several strategies can be implemented:
- Fume Extraction Systems: Implementing efficient fume extraction systems to capture welding fumes at the source can significantly reduce airborne contaminants, protecting both human operators and robotic arms.
- Protective Coatings: Applying protective coatings or finishes to robotic arms can enhance their resistance to rust and corrosion, prolonging their lifespan in welding environments.
- Regular Maintenance: Establishing a proactive maintenance schedule that includes cleaning, lubrication, and inspection of robotic arms can prevent buildup and ensure optimal performance.
- Environmental Monitoring: Monitoring air quality and particulate levels in welding environments can provide insights into potential risks and inform preventive measures.
Investing in a Fume Extraction System vs. Repair Costs for Robotic Arms
Investing in a high-quality fume extraction system for welding operations presents a proactive approach to mitigating potential repair costs for robotic arms. While initial costs for a robust extraction system may vary, ranging from several thousand to tens of thousands of dollars depending on size and complexity, it serves as a crucial investment in long-term equipment preservation. In contrast, repair expenses for robotic arms due to damage from welding fumes can be substantial, encompassing costs for corrosion and rust removal, mechanical repairs, and electronic component replacements. By prioritizing fume extraction, manufacturers not only protect the structural integrity and operational efficiency of their robotic arms but also minimize downtime and enhance workplace safety, making it a strategic decision for sustainable manufacturing practices.
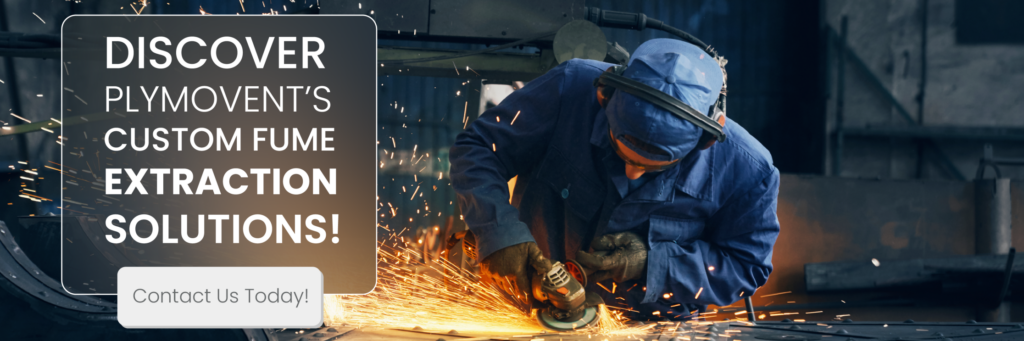
Plymovent Solutions
Plymovent systems are designed to capture and remove welding fumes directly at the source, thereby preventing them from settling on equipment and surfaces.
By integrating Plymovent solutions, manufacturers can enhance operational efficiency and prolong the lifespan of their robotic welding equipment.
Key Features of Plymovent Fume Extraction Systems:
- High Efficiency: Utilizes advanced filtration technology, including HEPA filters, to effectively capture welding fumes and airborne contaminants.
- Versatility: Designed for various welding processes and applications, ensuring comprehensive protection in diverse manufacturing environments.
- Compliance: Meets stringent health and safety regulations, providing assurance of regulatory compliance and workplace safety.
Plymovent offers tailored solutions that prioritize performance, compliance, and worker well-being. Embracing advanced fume extraction technology is not just a smart business decision but also a commitment to sustainable manufacturing practices and operational excellence.
By partnering with Plymovent, companies can leverage cutting-edge solutions to address the challenges posed by welding fumes effectively, ensuring long-term success and competitiveness in today’s dynamic industrial landscape.
In Summary
While robotic arms offer significant advantages in modern welding operations, they are susceptible to the harmful effects of welding fumes. Rust, corrosion, mechanical impediments, and electronic interference are among the challenges that can compromise their performance and longevity. By understanding these risks and implementing proactive measures, manufacturers can safeguard their investment in robotic technology and ensure sustainable and efficient welding processes.
In conclusion, addressing the impact of welding fumes on robotic arms is essential for maintaining operational efficiency, prolonging equipment lifespan, and safeguarding worker health and safety in industrial settings.
By prioritizing proper maintenance, implementing protective measures, and leveraging technological advancements, manufacturers can maximize the benefits of robotic welding while mitigating associated risks effectively. This holistic approach not only enhances productivity but also promotes a safer and healthier work environment for all stakeholders involved in modern manufacturing processes.
Comments are closed.